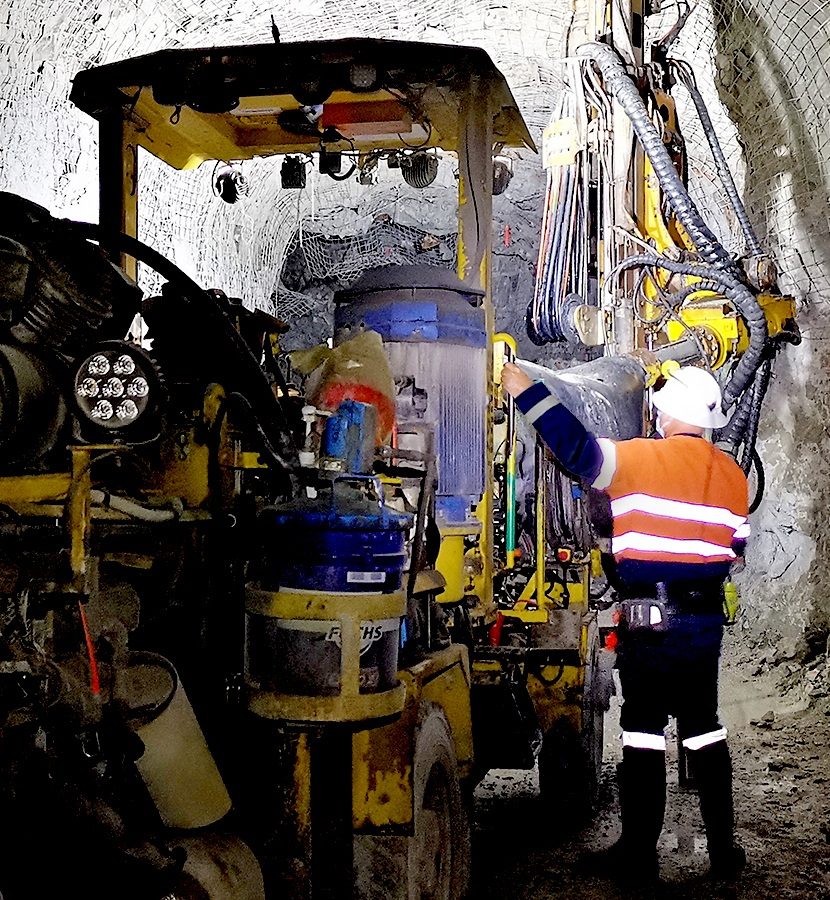
Cracow extracts $59M of Narrow-vein ore through drilling accuracy
In early 2018, the Cracow Gold Mine, located 500km North-West of Brisbane, knew they were facing challenges of dilution and stope performance attributed to inaccurate drilling. The drilling operations team decided to implement Minnovare’s Production Optimiser technology to address the challenge. The initial implementation led to an immediate reduction in blast-hole deviation, due to increased drilling accuracy and a subsequent 62% reduction in average dilution.
"Before the introduction of Minnovare’s Production Optimiser, very narrow stopes (<1.5M width) would have been uneconomical to mine. In 2018, the majority of stope designs were 2.5m to 3.5m, now they are 1.5M-2.5M. Cracow have been able to recover AUD$59M worth of gold ounces that were at risk due to the narrow vein nature of the stopes." Thao Nguyen, Senior Mining Engineer. Aeris Resources, Cracow Mine.
LOOKING BACK TO 2018:
Following the Production Optimiser’s successful implementation, Cracow engineers began experimenting with a new ‘ZIPPER’ drill pattern since the mine was facing very narrow stopes (<1.5M width) which would’ve been uneconomical to mine using the current DICE-5 pattern method. The aim was to replace the traditional DICE-5 pattern on the most narrow vein stopes. Due to the nature of the design, the Zipper pattern relies on a high degree of drilling accuracy – reducing the total number of holes drilled per stope and the average stope width to just 1.5m.
Two trial Zipper stopes were drilled and subsequently blasted. One of these stopes recorded 495 tonnes less dilution compared to what would have been mined using a traditional DICE-5 pattern. This represented an approximate 25% reduction in waste tonnes for the Zipper stope – which is a significant cost saving. Phil Jones, Cracow Senior Drill and Blast Engineer at the time stated: “We estimate that 10% of our stope tonnes going forward can now be mined using the Zipper pattern instead of Dice-5. At 390,000 stope tonnes per year, a similar 25% reduction equates to approximately 10,000 tonnes less waste/low grade ore that would otherwise have been hauled and processed. Which at current cost, works out to approximately AUD$1M (USD$0.7M) a year.”
FAST-FORWARD 2 YEARS:
Minnovare recently caught up with Thao Nguyen, Senior Mining Engineer at Cracow, now under new owners, Aeris Resources.
“Our stope sizes have dropped significantly over the years. Originally the majority of stope designs were much larger - 2.5m to 3.5m. Now, on average the majority of our stopes are 1.5m-2.5m wide. If a stope is 2.5m wide, we would still use the Dice 5 pattern. However, if we expect our stopes to be less than 1.5m wide, we use our Zipper pattern, with a hole spacing of 0.9m. To which, we add 0.3m planned over-break either side of the stope, making the designed width 1.5m wide. “That’s pretty narrow – typically equating just 2,000 stope tonnes. The margin for error is very fine, hence requiring a high degree of drilling accuracy. “Before the introduction of the Production Optimiser technology on our long-hole rigs, very narrow stopes such as these would have been difficult to recover economically.
THE RESULT:
Following analysis of Cracow’s reconciliation data for FY20 and FY21 stopes with <2,000 tonnes equated to 119 Stopes or around 53% of total production. Based on this, Cracow have been able to recover AUD$59M worth of gold ounces that were at risk due to the narrow vein nature of the stopes. The all-in cost of mining these stopes was approximately AUD$27M, generating an additional AUD$32M profit.
Thao Nguyen “That’s a big positive – ensuring we extract the maximum value possible over the remaining life of mine.”
In essence, the Production Optimiser has allowed us the flexibility to continue drilling optimally with both narrow vein and wider stopes, whilst also maintaining the accuracy from setup that we established back in 2018. Being agile to move between Dice-5 and Zipper pattern as needed has allowed us to maximise gold recovery and reduce dilution.
To view the full Case Study, visit HERE